This week, I have been shadowing the Quality Assurance/Control team at Gaia Herbs. The goal of the Quality team here at Gaia is to ensure that all products not only meet FDA and ICH regulations but that they pass the more rigorous standards set by the Gaia Herbs mission of Connecting Plants & People™. They do this by sampling and testing each batch of raw materials that come into the manufacturing process using the methods of analytic chemistry. This entails various forms of chromatography and spectrometry for determining chemical compositions of the herbal extracts, using statistical analysis as the guide for determining principal components and the presence or absence of adulterants.
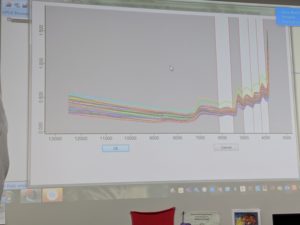
This week, I was able to review several of their methodologies and even got to gather data from their newest hemp product in the lab using FT-NIR spectrometry. This data was used to help build a chemical profile for the product, which will be used as a model to test against as the lab analyzes incoming product on a daily basis.
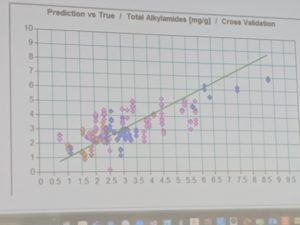
Several things that I was surprised by…
- Meet Your Herbs program
- This program allows Gaia product users to follow their herbal supplements from “seed to shelf.” The quality control team ensures that all customers can track the
- The size of the team needed for testing
- This department employs approximately 20 people for all of the QA/QC processes. This included approximately 12-15 scientists and several lab techs.
- The explicitness of SOPs and Methodologies
- Gaia, in their commitment to transparency, honesty, and quality, has created Standard Operating Procedures (SOPs) for each of their departments that describe, in detail, what each of the roles requires as team members complete their part of the supplement process. These, along with internal white papers that expand on their methodologies, provide a complete guide for processes within the lab.