Over the past few weeks at Bosch-Rexroth I have been engaged in multiple projects. I have worked on a “Bight Ideas” project, which are projects employees submit for improvement of processes in the company. The project I was assigned to was on the Mini-Rail line. The process in place was to label items that needed to be cut, deburred, cleaned, etc with a hand written sticky note. My task was to create and laminate cards for each of the processes that the company uses on this rail line. The first challenge I met was not understanding all the terms (deburring, mini-butt grind, etc) that were being referenced. I spent a couple of hours observing the mini-rail line and the processes. During my time working on this project I was able to observe how employees give input into the company and how their input is valued. This was a side to manufacturing that I didn’t originally know existed.
Another project that I worked on with Scott (another Kenan Fellow) was to problem solve an issue the company was having with the tables in their main conference demo room. The tables had a foot rest, but it didn’t have appropriate support so it would come loose each year. This particular bar had also been assembled upside down so when it needed to be tightened, the entire table had to be flipped upside down for maintenance! Scott and I felt like this was not the most efficient process. We first took off each foot rest on each table and flipped the foot rest bar the correct direction. We then measured for a supporting piece of the eco-shape tube to be cut and attached so that the tables will hopefully not need to be tightened as much as the past. This project helped us to get into the mindset of engineers. We jumped into the design process in the revision stage and after a few efforts had found what we felt was the best solution. The design process is one thing I have observed a lot of at Bosch Rexroth and will be incorporating into my classroom.
The final major project that Scott and I were tasked with was designing and creating an Eco-Shape Creation Kit (see picture below). We first did some research, learned the purpose of the project, and played around with the tubing and connectors to see how they work and function together. After we had an idea we drew out some sketches and created an EXCEL sheet to list the materials we would need. We learned the process for how to put in a material order to the Logistics Center and in a couple of days our materials had arrived. Before we could cut the aluminum, we had to be trained on the Kaltenbach Saw. We spent a few hours learning how to input measurements and operate the saw. We also wrote up user friendly directions for saw operation that Bosch will be using in the future for training interns.
The challenge with the Eco-Shape project was that since we had not built much with the materials before, we didn’t account for the added size caused by some of the connectors. This led to the base of the kit being too large for the container (oops!). We went back to our EXCEL sheet and revised our measurements. Bosch will be creating more of the kits we designed for their Community Outreach events. Side note, Scott and I each got to keep a kit for ourselves!
Overall my experience has taught me so much about the manufacturing world. I have learned the ins and outs of their processes, the value of logistics, the importance of having solid problem solving and communication skills. All of the things I have learned I will take back with me into my classroom.
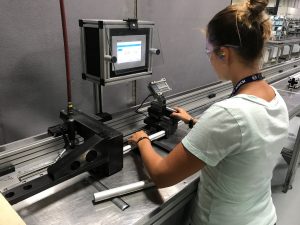
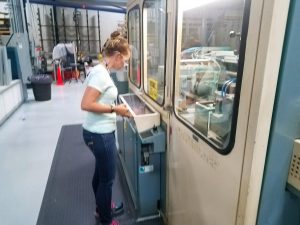
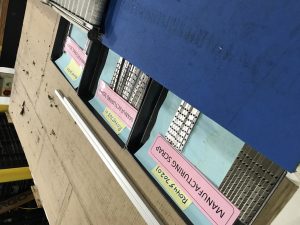
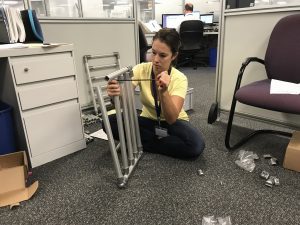
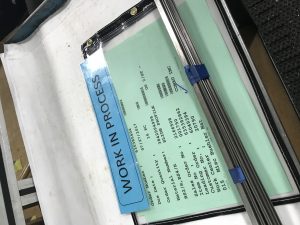